SILIMER series non-precipitation slip and anti-blocking masterbatch for food packaging film
The white powder precipitating on the food packaging bag is because the slip agent (oleic acid amide, erucic acid amide) used by the film manufacturer itself precipitates, and the mechanism of the traditional amide slip agent is that the active ingredient migrates to the surface of the film, forming a single molecular lubricating layer and reducing the friction coefficient of the surface of the film. However, due to the small molecular weight of amide slip agent, it is easy to precipitate or powder, so the powder is easy to remain on the composite roller during the film compounding process, and the powder on the rubber roller will be adhered to during the film processing, resulting in obvious white powder on the final product.
In order to solve the problem of easy precipitation of traditional amide slip agent, SILIKE has developed a modified co-polysiloxane product containing active organic functional groups - Silimer series non-precipitation film slip masterbatch. The working principle of this product is: The long carbon chain and the resin are compatible to play the role of anchoring, and the silicone chain migrates to the surface of the film to play a slip role, so that it can play a slip role without completely precipitation. Recommended grades: SILIMER5064, SILIMER5064MB1, SILIMER5064MB2, SILIMER5065HB...
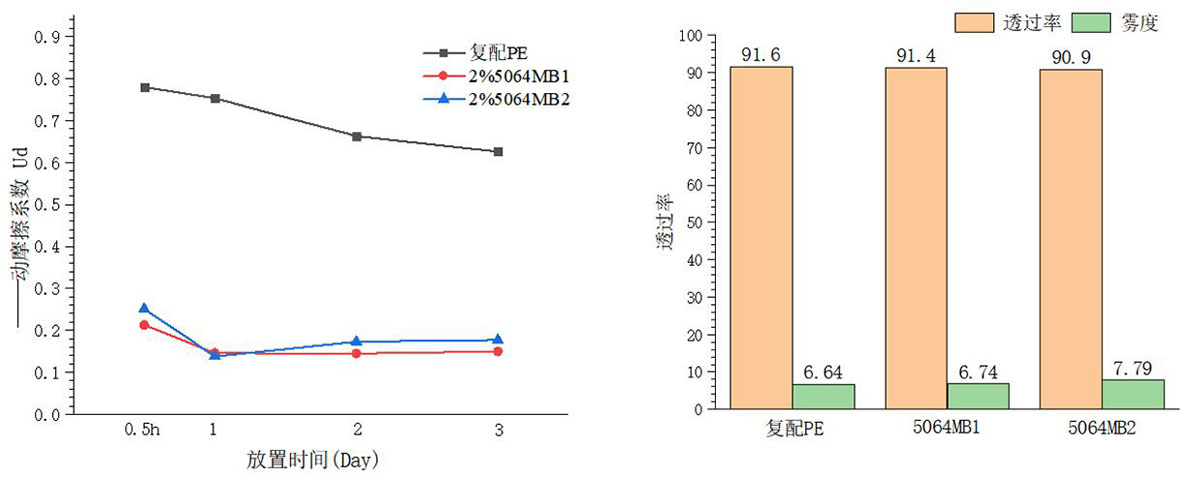
• Product typical benefits
• Good resistance to high temperature
• Long-lasting smooth performance
• Safe and odor-free
• Not affect film printing, composite, transparency
• Widely used in BOPP/CPP/PE/PP films......
• Some relevant performance test data
Effectively reduce the friction coefficient, does not affect the fog degree and transmittance
Simulated substrate formula: 70%LLDPE, 20%LDPE, 10% metallocene PE
As shown in Figure 1, the friction coefficient of the film after adding 2% SILIMER 5064MB1 and 2% SILIMER 5064MB2 was significantly reduced compared with the composite PE. Moreover, and as shown in Figure 2, the addition of SILIMER 5064MB1 and SILIMER 5064MB2 basically did not affect the fog degree and transmittance of the film.
• The friction coefficient is stable
Curing conditions: temperature 45℃, humidity 85%, time 12h, 4 times
As shown in FIG. 3 and FIG. 4, it can be seen that the friction coefficient of the film after adding 2% SILIMER 5064MB1 and 4% SILIMER 5064MB1 remains at a relatively stable value after multiple curing.
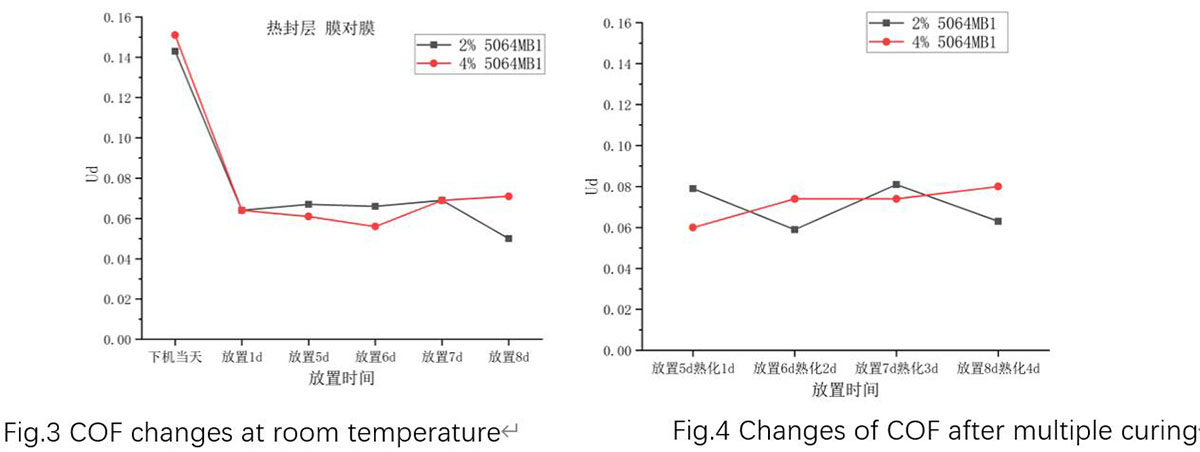
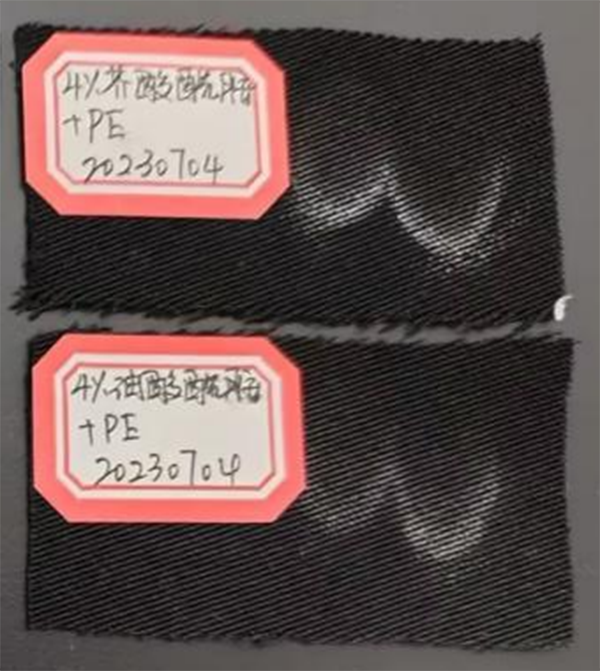
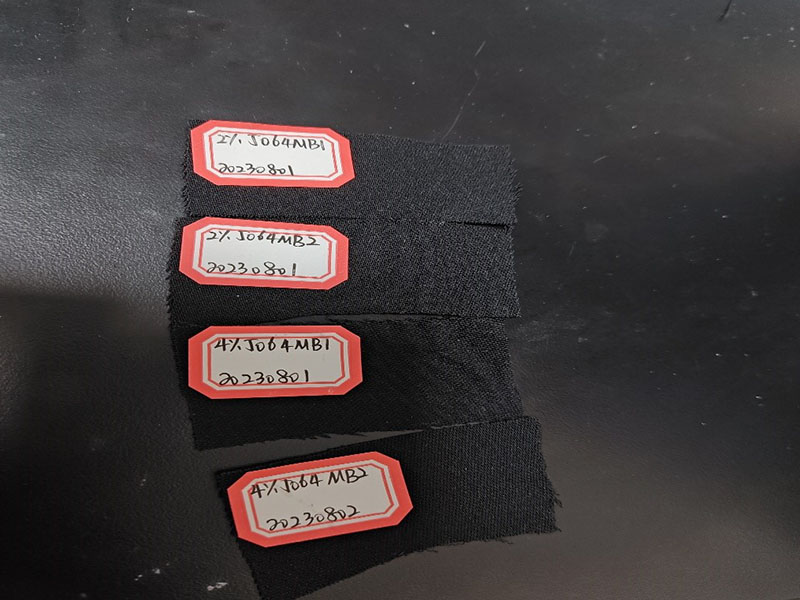
• The surface of the film does not precipitate and does not affect the quality of the equipment and the final product
As shown in the figure below, use black cloth to wipe the surface of the film with amide and SILIMER product. It can be seen that compared with the use of amide additives, SILIMER series does not precipitate adn has no any precipitating powder.
• Solve the problem of white powder in the composite roller and the final product bag
As shown in the figure below, after the composite roller passes 6000 meters of the film with erucic acid amide, there is obvious accumulation of white powder, and there is also obvious white powder on the final product bag; However, used with SILIMER series we can see when the composite roller passed 21000 meters, and the final product bag was clean and fresh.
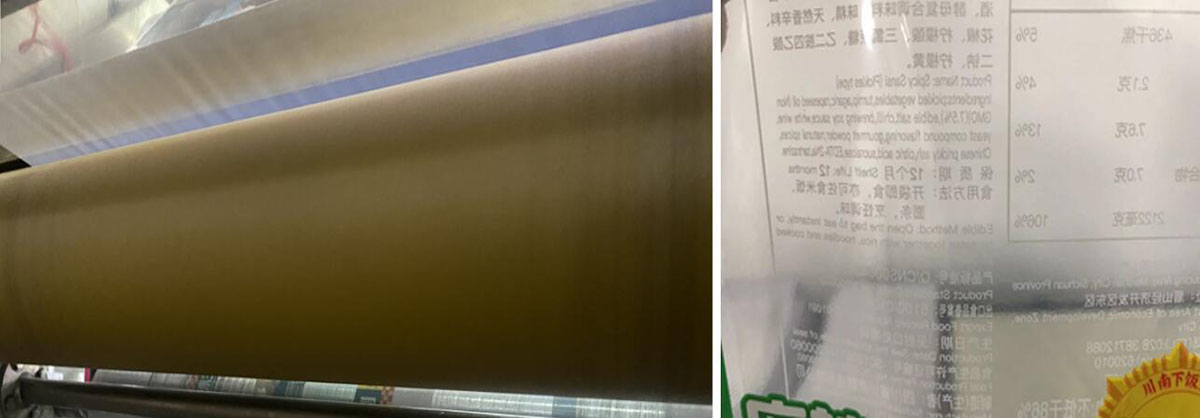
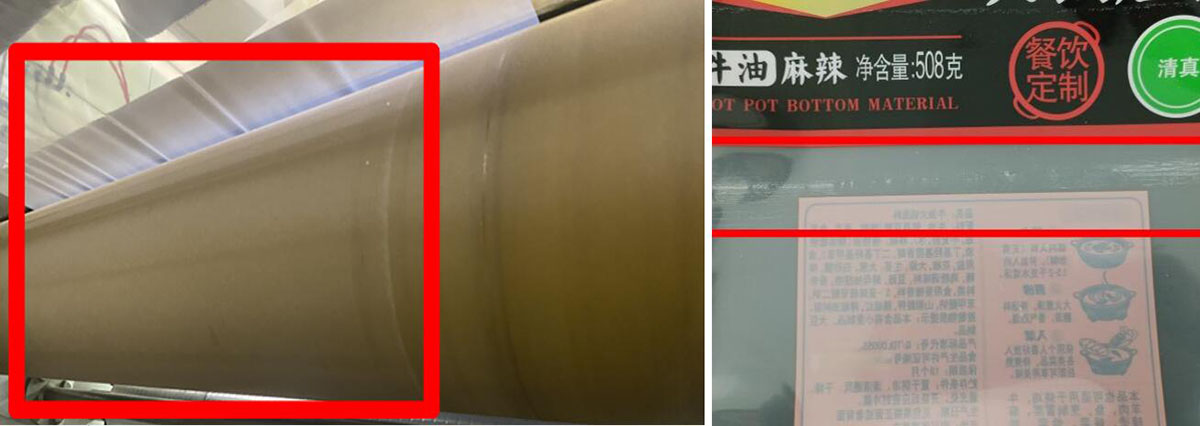
Adding Silimer series
Adding amide
SILIMER no precipitation film slip masterbatch, keep the first door of food safety, ensure the safety of food packaging responsibility! If you meet any queries about food packaging bags or other films, please contact us, we will be happy to customize solutions for you!